Value Chain
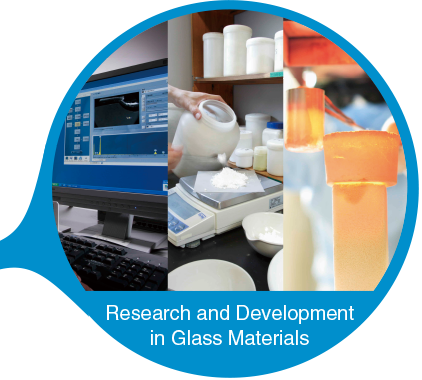
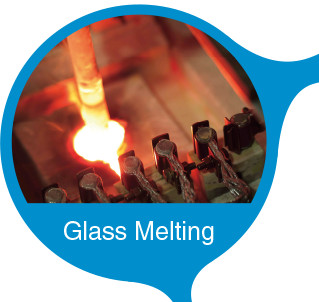
Glass Melting
After blending raw materials to attain the required optical quality, the batch is melt at 1,200 to 1,400℃, depending on the type of glass composition. Annealing, controlled temperature reduction, follows to condition to obtain the appropriate properties.
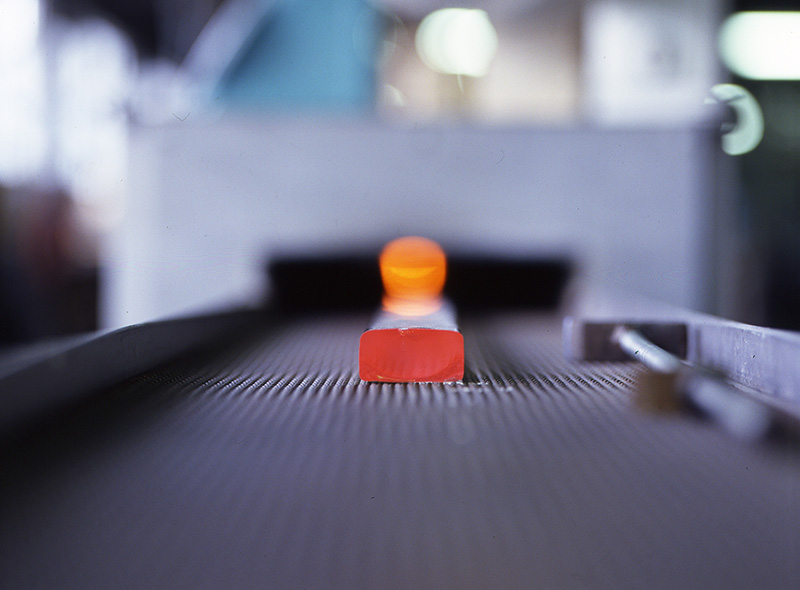
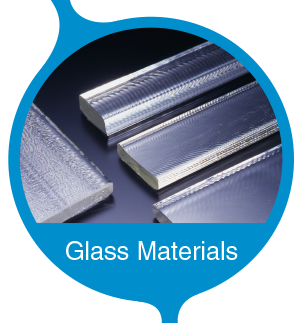
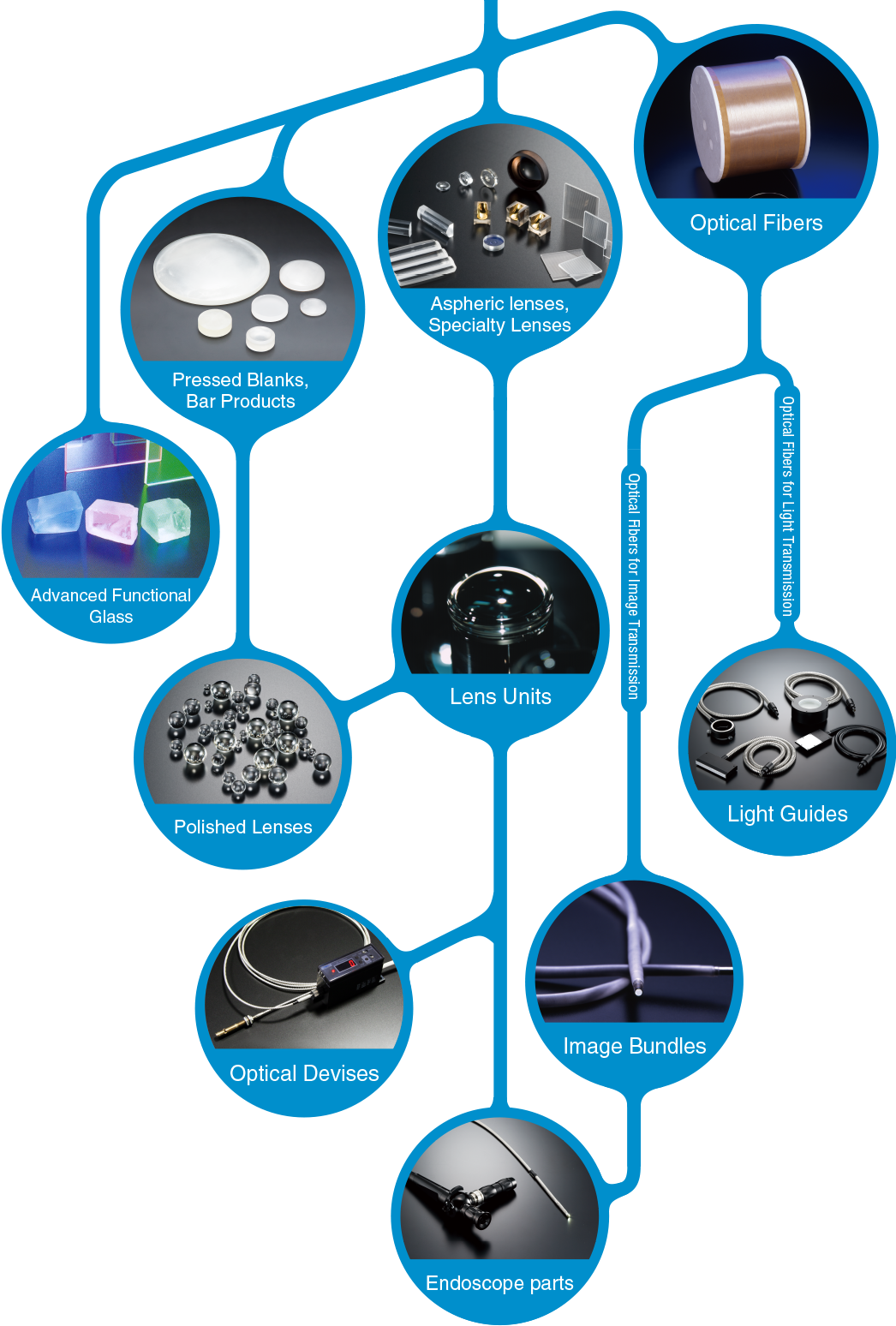
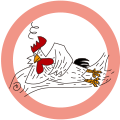
Drawing fibers
Core and clad glasses are melt in a double structure crucible. A fiber is drawn through the bottom surface of the crucible from the melted core and clad glasses. Since outer diameter of a fiber is determined by the drawing speed and temperature conditions, it requires precise control. We produce fibers of outer diameter from 30 μm to some hundred μm.
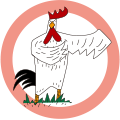
Ultraprecision molding die processing
A Molding die is manufactured to correspond the accurate shape of lens.
Forming
Load the preforms onto a molding die, and press while heating. Then, cool them slowly, and takeout the lenses. SUMITA is capable of manufacturing aspheric lenses which outer diameter of less than 0.5 mm to about 30 mm.
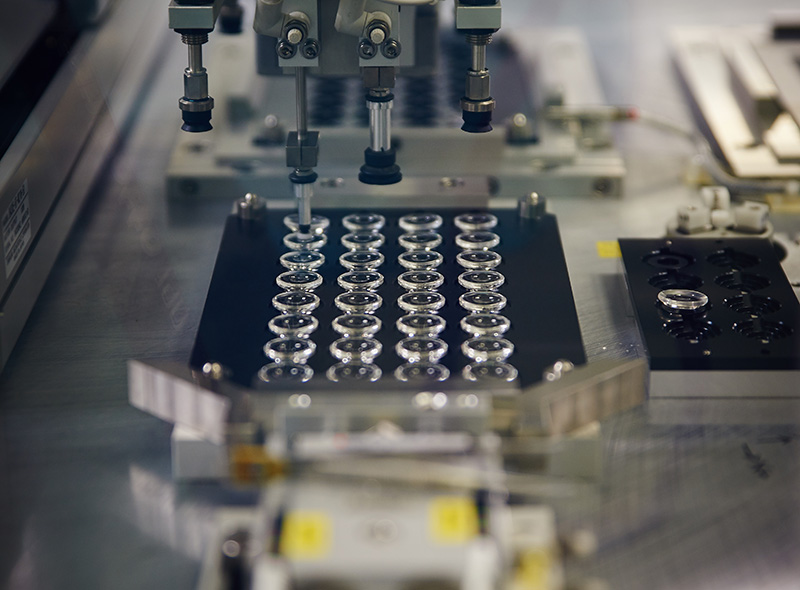
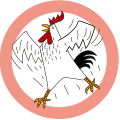
Lens Units Assembly
We carry out the precise assembly of lenses. A slight error in alignment can cause optical axis misalignment, and affect image quality. Alignment and assembly of lenses need precise assembly techniques.
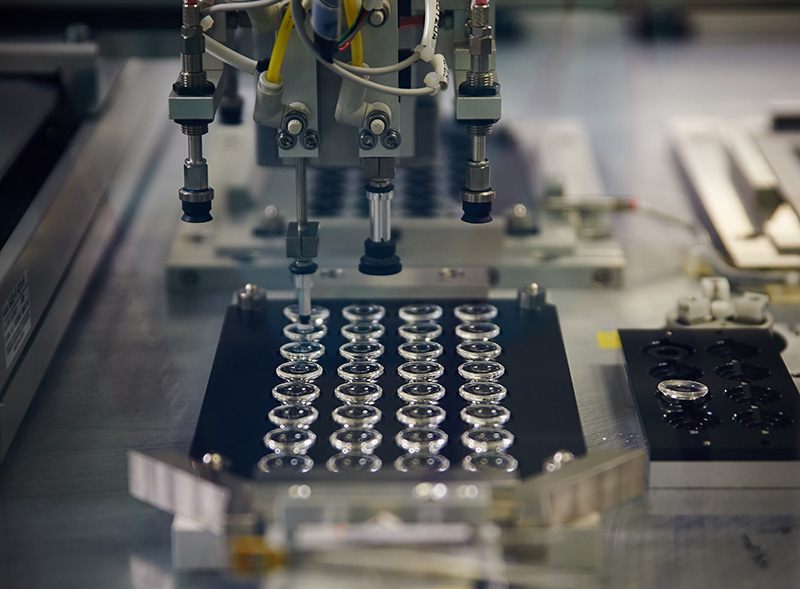
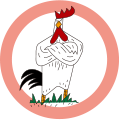
Fiber Assembly and Randomization
We randomize bare fibers to meet customer’s needs. Randomization needs skillful technique and expertise, since it arranges fibers without breaking. (The individual fiber is as thin as a human hair.)
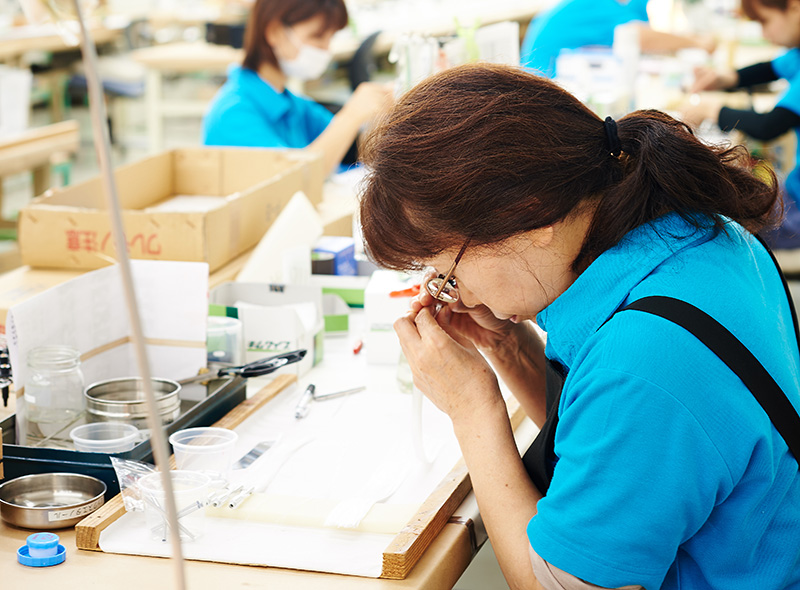
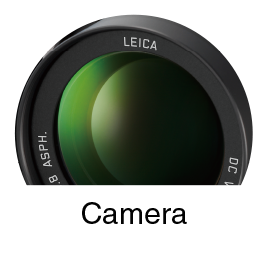
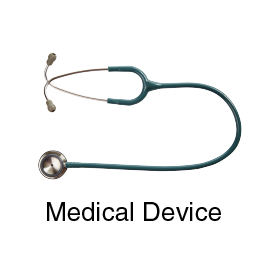
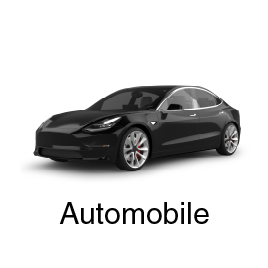
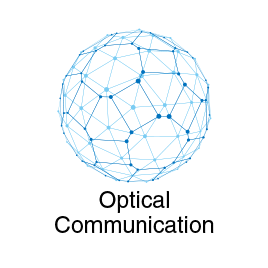
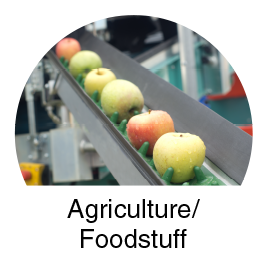
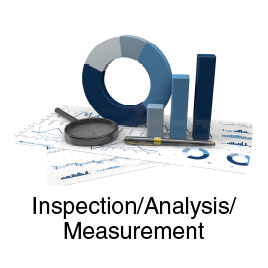
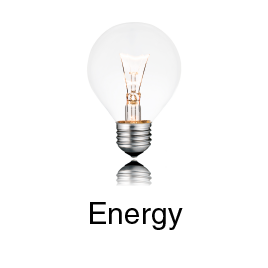
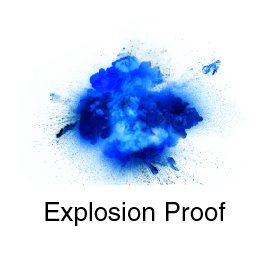
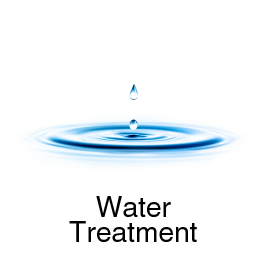
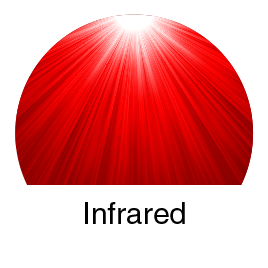
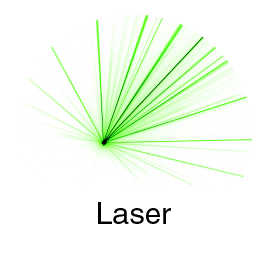