開発ストーリー
日々新たな製品を研究している開発者の声をお届けします
STORY 01電池材料
SELAPath(セラパス)
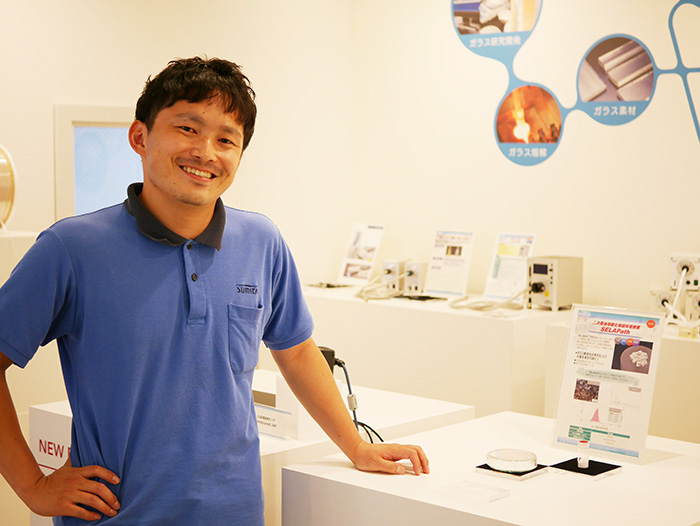
T・T
* この酸化物結晶は化学式Li1.4Al0.4Ti1.6(PO4)3(略称:LATP)で表されます。
LATPは、リチウムイオンを伝導させることのできる固体材料として古くから知られており、当社では1990年代からガラスを元にLATPを作る研究を行い、その使い道を探っていました。当時から、リチウムイオン二次電池の固体電解質として使えるのではないかという開発テーマで細々と検討を行っていました。
SELAPath開発者のストーリーとSELAPathの特長を紹介します。
SELAPath(セラパス)が誕生するまで
SELAPath開発のきっかけを教えて下さい。
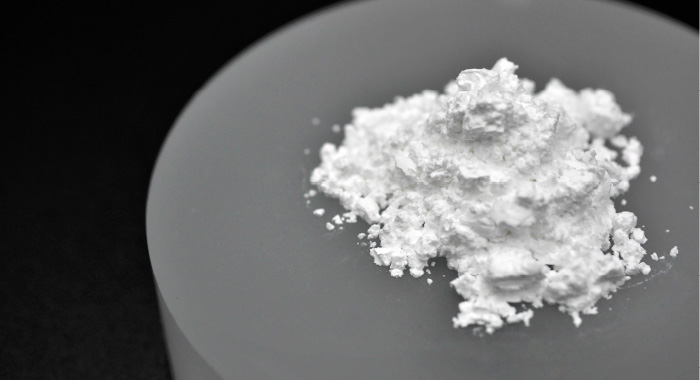
入社してまもなく、電池材料用途の開発テーマを上司から引継ぎました。私の作った組成がたまたまうまくいったことで、本格的にこのテーマに取り組むようになりました。当時、電池の安全性(可燃性)が問題になっており、電解質に不燃性のセラミックスを採用する全固体電池が着目されていました。
開発は順調に進んだのでしょうか。
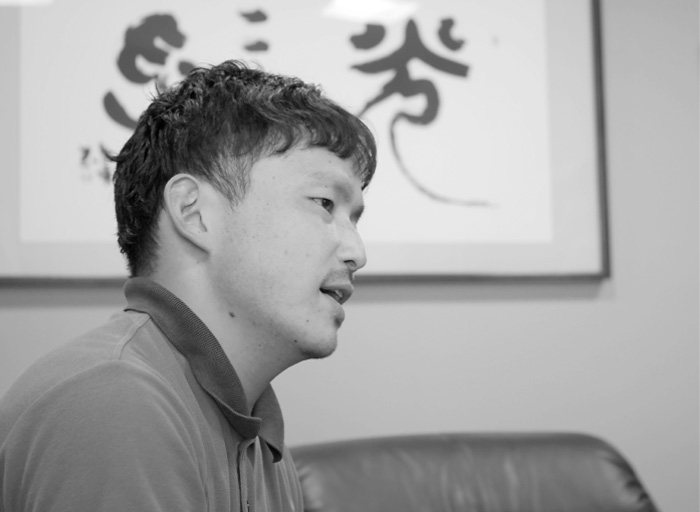
既存の材料の組成を変える程度でしたので、材料組成の開発は難しくはなかったです。大変だったのは、それを量産化するプロセスでした。小スケールの実験室レベルでは問題がないものも、大規模なスケールになると影響が大きくなり、問題になる点が出てきます。お客様に安定供給するための量産工程を確立するところがもっとも難しかったですし、今も安定した品質でお客様に提供できるように注意を払っています。
SELAPathについていえば、私が注力してきたことは製造プロセスの開発と捉えています。
具体的にどのあたりが課題だったのでしょうか。
SELAPathはガラスからLATPを合成する当社独自の製法(ガラス結晶化法)で作られています(特許申請中)。SELAPathのもとになるガラスは特殊で、光学ガラスと基本的な製法は同じですが、製造工程が異なるところがあります。製造のための炉や環境なども、大量生産を行う場合には、研究室レベル・少量試作とは別のものになります。
量産にあたっては、高品質なガラスを作製するために熔解条件を変えたり、工場の技術者と協力して製造工程を検証したりしながら、課題を一つ一つ克服していきました。製造プロセスはテクニックを要するところなので詳細は伏せますが、量産化のための製造工程の確立が最も注力した点と言えると思います。
量産可能な製法を確立できた背景にはどのような要因がありますか。
当社では、抗菌剤の需要が高まった時期に、LATP-Ag(抗菌剤)を販売していたこともあって、LATP-Agから派生する形で電池材料として使えそうかどうか、お客様数社からお問い合わせを頂いていたことも量産技術の確立を後押ししました。今回、SELAPathの経験を通じて、早い段階から量産案件に携わることができて良かったです。お客様の立場に立って、量産前提で開発を進めていく重要性を理解することができました。いま取り組んでいる別の案件も、量産を視野に入れて開発をしています。
SELAPathの特長
SELAPath(セラパス)の特長・強みについて教えて下さい。
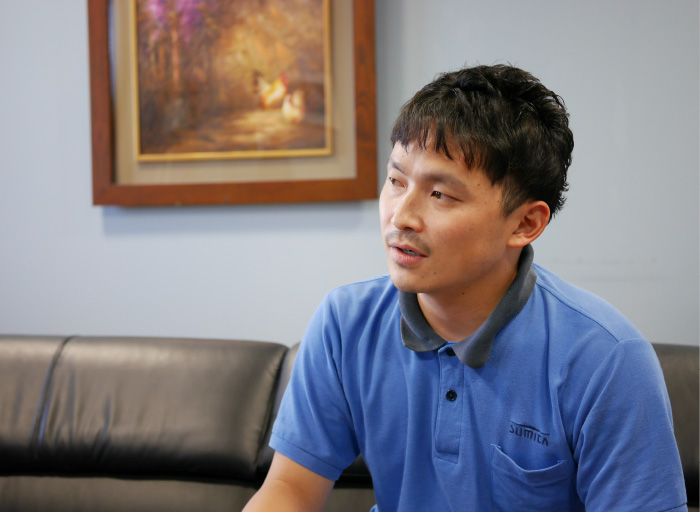
まず量産性・価格優位性です。材料として目新しいものではないため、イオン伝導度についていえば特別高性能というわけではありませんが、取り扱いしやすく、安全性が高く、安価で提供できます。
現時点で150kg/月程度の生産が可能で、生産体制を整えれば1トン/月も可能です。この規模の量産が可能なメーカーは現時点では他にないと思います。
ある製品・技術を市場に普及させることを考えた際、性能が優れていても取り扱いが難しい・価格が市場に合わない等の要因がネックになることはあると思います。全固体電池も含めて、新しい技術の実用化にあたっては、どの材料を採用する場合であっても、普及にはその価格が市場のニーズとマッチすることが重要です。その点、SELAPathは取り扱いしやすく、量産規模の拡大による低コスト化が可能、という利点は、お客様の製品の実用化と普及の観点から大きな意味を持つと考えています。
取扱いが難しい、というのは具体的にはどのようなことでしょうか。
固体電解質の材料を例にとると、イオン伝導度が高いものであっても、大気中で取り扱いできず、耐水性が低い、有毒ガス発生のリスクがあるなどの理由で、高度な生産設備が必要になるものもあります。LATPは酸化物なので大気中で取り扱い可能です。
その他の特長はありますか。
品質面でいえば、SELAPathは粒子形状が揃っていること、特別な製法により粉砕によるコンタミネーションがないという特長があります。
- SELAPath粒子形状
- 一般的なセラミックスの製法(固相法)と比べると、当社の製法(ガラス結晶化法)で作製したSELAPathは以下の特長を有すると言えます。
- 粒子形状/サイズが揃っている
- 製法上、粉砕によるコンタミネーションがない
SELAPathの特注対応は可能ですか。
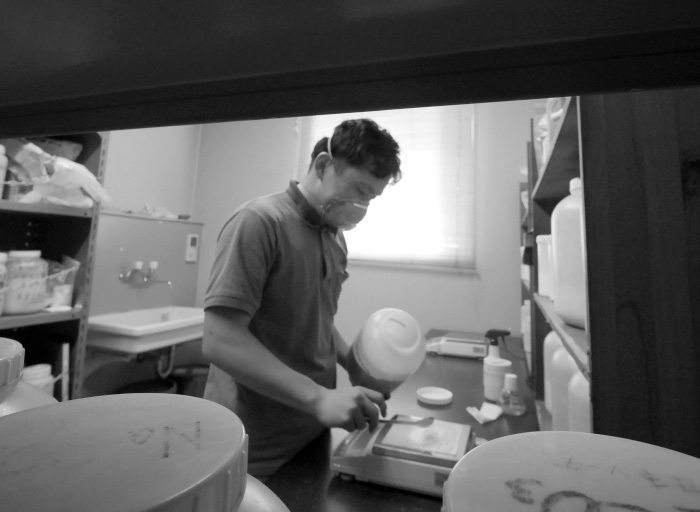
標準品の基本提供形態は粉体です。粒子サイズについては、粉砕なしである程度コントロールすることはできます。また、お客様のご要望に応じて組成の微調整も可能です。
なお、(特注ではないですが)当社に製造設備は揃っていますので、量産にお困りのお客様からの受託熔解のような対応も承ります。
どのようなお客様にSELAPathを使っていただきたいですか。
SELAPathは全固体電池材料としてPRを始めましたが、全固体電池やその他の電池に限らず、できるだけ広い分野・用途に検討していただければと思っています。私たちが知らないだけで、まったく別の用途で使えるかもしれません。私たちのスタンスは、「このような材料ができました。量産可能な工程を確立し、安価で提供できます。興味があったらぜひ使ってください」というものです。お客様から、この材料を試したい、使えるかもしれない、新たな材料を開発してほしい、というようなお話があれば、お客様と一緒に課題解決をしていきたいです。お客様に材料をうまく活用していただき、お客様のビジネスをさらに前に進めるお手伝いができたらとても嬉しく思います。
住田光学ガラスの研究開発
研究開発テーマはどのように決めるのでしょうか。
当社では、研究者が自主的に研究テーマを考えて開発していくものと、お客様からの引き合いを受けて開発を進めるものの双方向の開発があります。私はどちらも重要だと考えています。自分たちだけだと材料に対する具体的なニーズは分からないですから。課題は明確な方が解決しやすいですし、課題を解決できればお客様に使っていただけます。両方あるべきだと思っています。
開発者としてやりがいを感じるのはどのようなときですか。
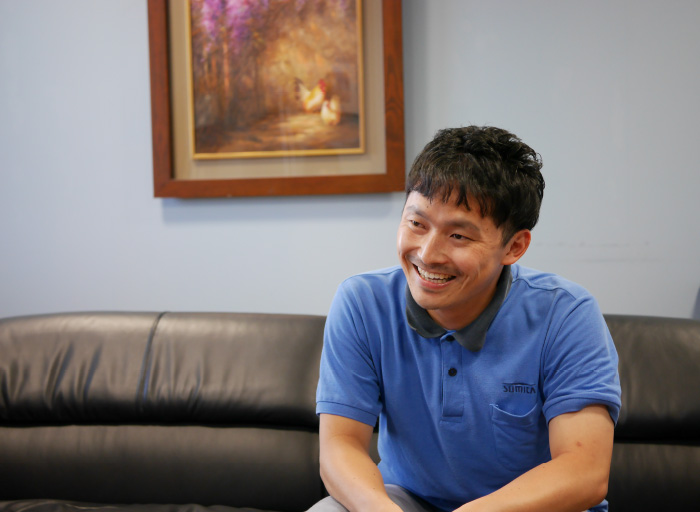
開発した材料をお客様に使っていただけたときは本当に嬉しいです。開発した材料が日の目を見たとき、開発者冥利に尽きると感じます。
現在取り組んでいること、
今後の展望を聞かせて下さい。
現在取り組んでいることは、光学ガラス開発がメインです。住田光学ガラスという会社が光学ガラスから始まったこともあって、コンスタントに取り組んでいます。最近は、LATP関連の開発が大きな割合を占めるようになってきました。新しい材料や、もう少し特性を上げられないかというような開発をしています。
ガラス結晶化技術は奥が深く、さらに可能性があると感じています。ある程度研究を続けていると、組成や結晶化させるところなど、コツというか傾向のようなものが見えてきます。最終的に作りたいものに応じて、析出させる結晶の種類や量、大きさなどの制御の方法、組成・熱処理工程の調整など、うまくいく組み合わせがあると感じています。
これからもこの技術を生かして別の用途に応用していきたいです。K-VC89(通信用レンズ材料)のような、世の中で広く使っていただき業界のスタンダードになるような材料を開発できたらいいなと思っています。
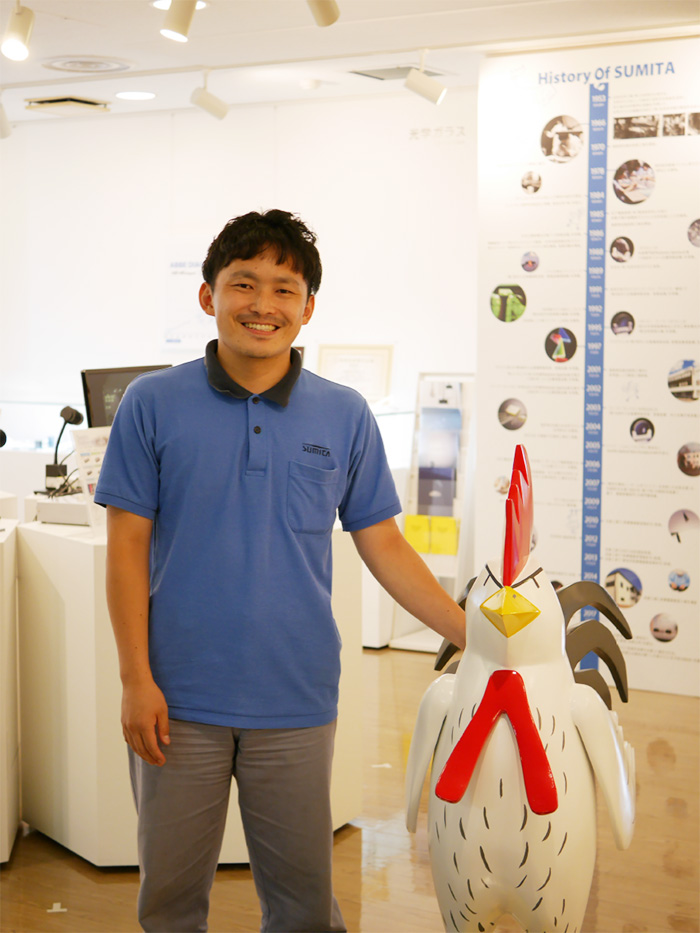